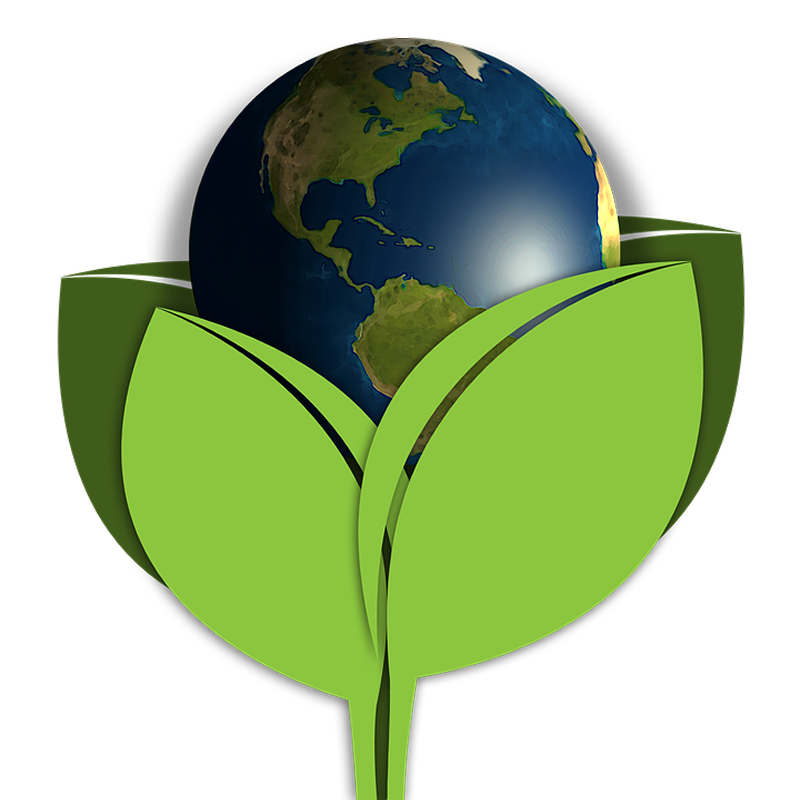
CED’s journey to a greener future for business
The environment is everything they depend on, and as with all businesses, BALI Registered Affiliate CED Stone Group have a legal duty to conduct business activity in a manner which protects it. At CED they realise it’s not just a legal duty but also a responsibility and are constantly striving to improve our working processes and habits to conserve and protect the environment.
Across their six nationwide depots they identified two main environmental concerns, wood waste, and dust.
Wood
You might not expect a natural stone supplier would have an issue with wood waste, but company-wide CED Stone Group handle hundreds of thousands of tonnes, of stone materials a year. A large proportion of our materials such as paving and setts come in crates and on pallets leaving them with hundreds of tonnes of wood waste a year.
CED Stone Group will get as much use out of crates and pallets as they can but when they become unfit for purpose the wood waste at each individual depot is segregated and collected by a reputable company for recycling. Wood tends to be recycled into mulch or pulp and can be used beneficially as fuel.
Dust
Their second main environmental concern across the depots was air pollution, in the form of dust. Solving this issue was not an easy task considering the hundreds of thousands of tonnes of stone material previously mentioned, all come coated in the stuff.
To keep the levels down in the yards we employ dust suppression trucks which tend to the depots during the summer months when the dry weather worsens the problem. The biggest culprit they found for dust emissions in the depots was the robotic bagging plants, which they have at their Scotland and London East depots.
In the bagging plants gravels, aggregates, pebbles etc are subjected to vigorous motion resulting in a great deal of powder being expelled. To remedy this CED Stone Group had a new dust extractor system fitted to their Castlecary Depot’s robot line in 2017 and West Thurrock’s is due to be installed by the end of this year. These systems are a major investment for CED Stone Group, but will greatly reduce the amount of dust being released into the atmosphere.
Packaging
At the start of 2019 they said goodbye to plastic bubble wrap and switched to a 100% recyclable, renewable and biodegradable packaging solution for sending out their many samples. It might not seem that important but last year they used 1700m2 of bubble wrap, this is one and a half times the size of an Olympic swimming pool, and believe it is something to shout about.
A little done by a lot
There is a lot of small things they do as a company too. For instance, changing light bulbs to energy saving LED bulbs, using biodegradable brochure bags, printing double-sided whenever possible, and holding meetings on Skype to cut down on travel and fuel emmissions. These little things might not seem like much but little things practiced by a lot can and does make a difference.
ISO 14001:2015
Thanks to all the improvements they have made, and to the dedication and hard work from managers and staff across all six nationwide depots and head office, at the end of last year we were delighted to be awarded our ISO 14001:2015.
‘ISO 14001:2015 is intended for use by an organization seeking to manage its environmental responsibilities in a systematic manner that contributes to the environmental pillar of sustainability.’
We know this is just the start and that there is much more we can do, and our company and those that work in it are committed to carry on reducing our impact, and caring for our environment.