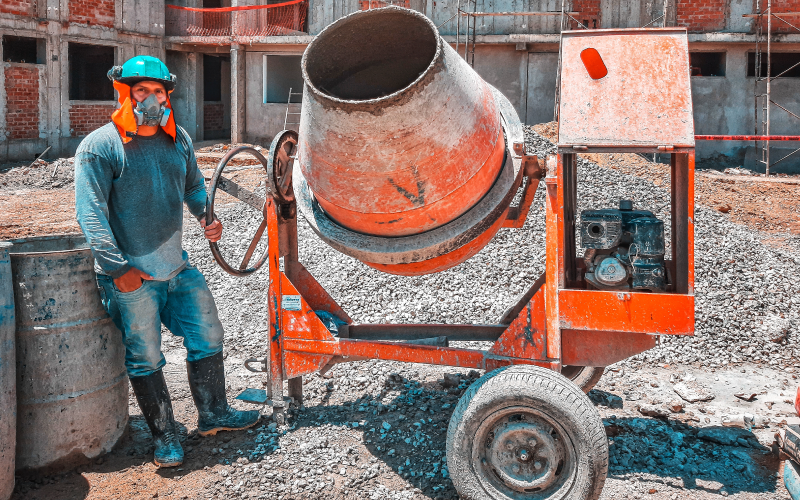
Plant Provision and Use of Work Equipment Regulations 1998 (PUWER)
PUWER is regularly referred to by the Health and Safety Executive (HSE) in accident reports. But what is it? And how is it relevant to the landscape industry?
In March 2022 a company was fined for failure to maintain a large dumper truck; the brakes failed during work on a construction site and the driver lost control. The dumper rolled backwards from the worksite across a busy road and tipped on its side, injuring the driver. The cause of the accident was faulty brakes, which the hire company had failed to maintain in accordance with the manufacturer’s guidance.
This is an extreme example but outlines why regulations such as PUWER are necessary.
PUWER places duties on people and companies who own, operate, or have control over work equipment. PUWER also places responsibilities on businesses and organisations whose employees use work equipment, whether owned by them or not.
The term ‘work equipment’ is very broad, and includes any machinery, appliance, apparatus, tool or installation for use at work (whether exclusively or not). This includes equipment which employees provide for their own use at work.
PUWER requires work equipment to be:
- suitable for the intended use
- safe for use, maintained in a safe condition and inspected to ensure it is correctly installed and does not subsequently deteriorate
- used only by people who have received adequate information, instruction and training
- accompanied by suitable health and safety measures, such as protective devices and controls. These will normally include guarding, emergency stop devices, adequate means of isolation from sources of energy, clearly visible markings and warning devices used in accordance with specific requirements, for mobile work equipment and power presses
What do you need to do?
PUWER has a particularly broad remit, but the landscape industry should be mindful of the following areas of the regulation:
- ensure work equipment is only used for suitable purposes
- ensure work equipment is maintained in an efficient state, in efficient working order and in good repair
- where a machine has a maintenance log, keep this up to date
- where work equipment is exposed to deteriorating conditions liable to result in dangerous situations, it must be inspected to ensure faults are detected in good time so the risk to health and safety is managed
- ensure that all people using, supervising or managing the use of work equipment are provided with adequate, clear health and safety information. This will include, where necessary, written instructions on its use and suitable equipment markings and warnings
- ensure that all people who use, supervise or manage the use of work equipment have received adequate training, which should include the correct use of the equipment, the risks that may arise from its use and the precautions to take
Further Reading
Written by Owen Baker | Technical Officer